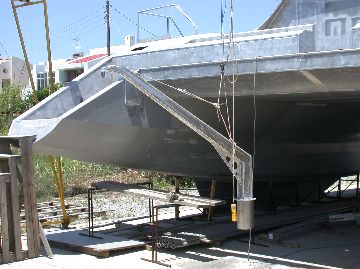 |
... hier noch am Kran ... |
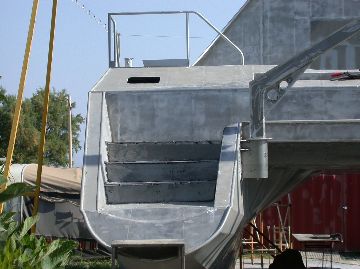 |
... und jetzt fest verschweißt. |
Als nächstes habe ich dann meine Ruderwellen vom Petro, einem
sehr gutem Dreher oberhalb der Stadt, drehen lassen. Nun konnte ich
die Ruderblätter bauen und die Ruderlager und das Fundament für
den Hydraulikzylinder fertigstellen. Danach hat dann das Heck seine
endgültige Form durch die Fertigstellung der Treppe erhalten,
inklusive einer Revisionsluke.
Hier nun die Bilder in Einzelschritten dazu:
|
|
Ruderwelle STB :
Material: Alu
1350mm lang,
Durchmesser
70 bis 50 mm
am oberen Ende
mit Gewinde und
vierkant-Kopf
|
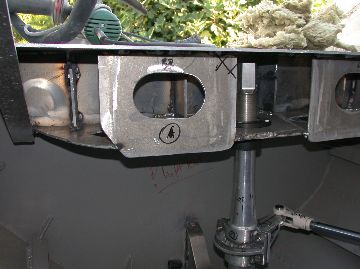
|
Unteres Lager
(70mm), selbstausrichtend, im Rumpfboden mit Steifen fest verschweißt.
Oberes Lager (50mm) in der Treppenkonstruktion
verschraubt |
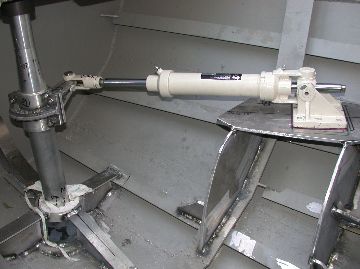 |
Hydraulik-
Lenkzylinder-
Fundament auf
BB-Seite |
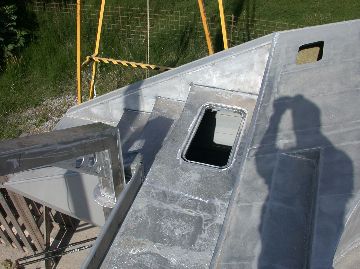 |
Die fertige Treppe
auf BB mit Inspektionsluke.
Unter der Treppe ist außer dem Ruder später auch
noch der Elektromotor für den Antrieb bei Flaute.
Einen weiteren Zugang gibt es durch die Luke im Schott vom
Rumpf innen.
STB-Seite ist natürlich identisch. |
Jetzt konnte der Bau der Ruderblätter beginne.
Bei meinem Freund, Mafio, der an der Kantbank gegenüber
arbeitet, habe ich die vier Seiten der Blätter vorbiegen
lassen. |
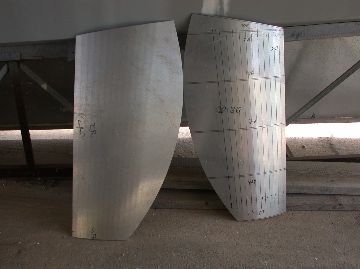 |
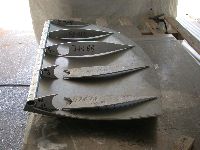 |
... dann konnten die Steifen eingesetzt werden, die auch mit
der Ruderwelle verschweißt sind. |
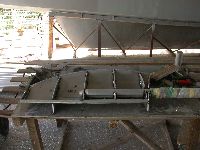 |
Für den "festen Stand" auf der Arbeitsplatte
hatte ich extra eine Form gebaut. |
Hier ist schon eine Seite des ersten Ruders fertig ausgerichtet
und verschweißt. |
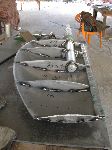 |
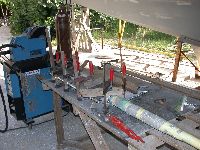 |
Nun konnte die zweite Ruderblattseite angeheftet werden. Damit
sich nichts verschiebt wurde alles fest mit Zwingen gehalten. |
Hier nun die fast fertigen Ruderblätter.
Es fehtl nur noch ein wenig Schleifarbeit und Spachtelmasse,
damit dann später das Wasser auch ohne Verwierbelungen
daran vorbeifließen kann.
Um die Ruder jetzt einzubauen, muss ich erst noch ein kleines
Loch in meine Betonplattform stemmen, denn mit der Ruderwelle
ist das ganze im Moment zu lang.
Allerdings muss ich noch auf zwei Spezialmuttern aus V4A und
zwei Keile warten, bis die Ruder endgültig montiert werden. |
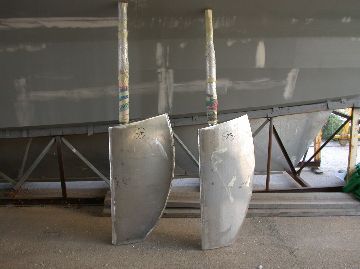 |
Zwischendurch war immer wieder mal Zeit für "Kleinkram",
wie z.B. Poller und Klüsen bauen. Oder Griffe und Riegel für
die Decksluken und Fenster und den Ruderarm oder Borddurchlässe
für Auspuff, Salzwasserzufluß und Abwasserabfluß
u.s.w.
Kleine Serienproduktion:
- Festmacherpoller
- Lukengriffe |
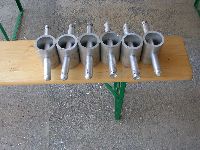 |
|
|
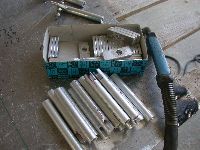 |
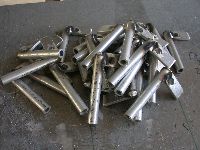 |
|
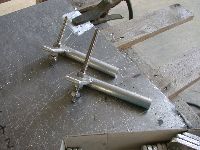 |
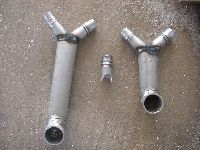 |
... Borddurchlässe |
...Ruderarm |
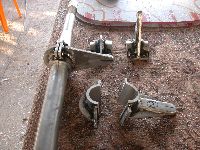 |
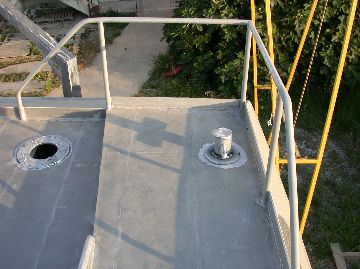
|
Poller und Winschfundament auf BB-Seite |
|
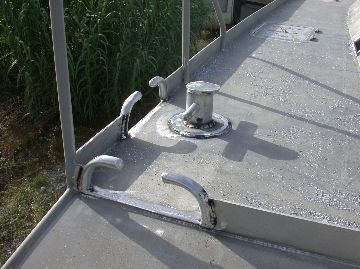 |
Dann kam endlich meine Ankerwinsch aus Deutschland. Der Transport
nach Kreta hatte sich etwas verzögert. Also rauf auf den Kat
und ab damit nach vorn in die Vorschiffsluke vorm Mast. NAchdem das
Fundament fertig war konnte auch die Kettenführung in Rohren
durch den Katwalk fertiggestellt werden und das letzte "Loch"
im Deck geschlossen weden.
|
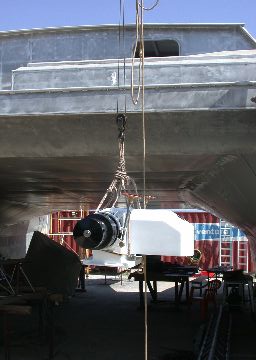 |
Fundament der Ankerwinsch im Vorschiffsluk vor dem Mast im
Brückendeck
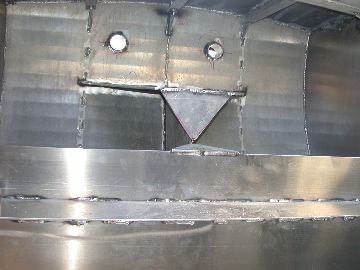
|
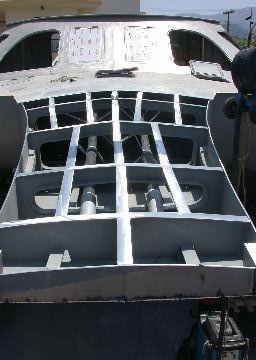
|
Nun war es an der Zeit mit dem Bau des Gitter-Rohr-Mastes zu beginnen.
Aus 6m langen Edelstahlrohren (60,3x2,9mm) und Streben aus Rund 15mm
besteht diese Konstruktion. Insgesamt ist der Mast 21,3m lang. Besteht
also aus 4 Teilstücken, dem Mastuß, den Beschlägen
für die Unterwanten und dem Masttop.
Damit beim Edelstahlschweißen das Schutzgas auch in der Inneseite
der Rohre beim Schweißen seine Wirkung erziehlen kann, habe
ich die Rohre mit Schutzgas (Argon) gefüllt.
Diesen Tipp habe ich von einem Schweißfachingenieur aus Berlin,
der auch gerade einen Katamaran baut - aber aus Holz.
Als Baugerüst diehnten meine gleichhohen Gestelle, die ich dann
noch mit der Wasserwage und Schnüren ausgerichtet habe, damit
auch alles gerade wird.
Hier nun die BIlder dazu:
|
Nach dem Grundieren und Lackieren der einzelnen Teilstück
habe ich mit hilfe eines Kettenflaschenzuges die 4 Mastteile
zusammengezogen, verschweißt und die noch fehlenden Diagonalstreben
eingebaut. Später habe ich dann noch die Verbindungstellen
ebenfalls grundiert und lakiert.
Nun wartet der Mast auf BB-Seite auf das Aufstellen mit dem
Autokran. |
In Vorbereitung für den Bau und die Montages
des Bugbeams habe ich zunächst die dazu nötigen Halterungen
aus 20 mm dicken Aluplatten ausgesägt und zusammengeschweißt
... |
|
... dann die Positionen an den Rumpfinnenseiten ausgemessen
und festgelegt ... |
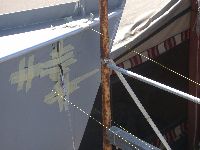 |
|
... und angeschweißt. |
Dann kamen endlich meine "dicken" Edelstahlrohre für
den Bugbeam aus Deutschland. Jetzt konnte ich den Gitterrohr-Bugbeam
auch als "Drei-Bein" wie den Mast, bauen. Ein Probeweises
anhängen mit Kranhilfe ermöglichte es mir die genauen
Positionen der Katwalk-Lagerbleche am Beam zu bestimmen und anzupunkten. |
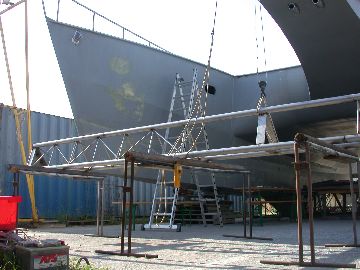
|
 |
|
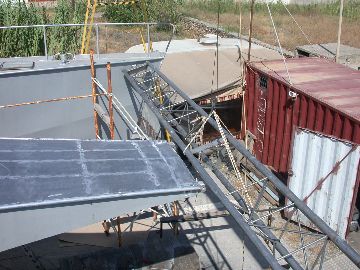 |
...jetzt muss der Beam noch ein mal wieder runter um alles
komplett zu verschweißen.
Dann noch wie schon den Mast, Grundieren und Weiß Lakieren
und fertig montieren.
Aber diese Bilder gibts dann erst beim nächsten mal zu
sehen. |
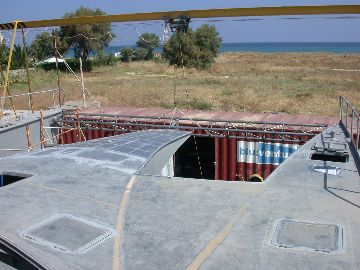 |
Inzwischen ist auch das Katwalkdeck geschlossen und angeschliffen.
So wartet es auf die Grundierung zusammen mit dem restlichen
Deck.
Auch hierzu gibst die Bilder im nächsten Bautagebuch. |
|
|
|
|
So das wars mal wieder.
Wie der Mast gestellt wird und das Rigg dann ausehen wird inklusive
dem dann fertigen Bugbeam gibts im nächsten Bautagebuch zu sehen.
Wenn alles klappt wird es auch wieder einen kleinen Film zum Maststellen
geben.
Ende der ersten Halbzeit der Arbeits-Saison 2007
|